The manufacturing process for printed circuit boards (PCBs) requires a complex set of steps and attention to detail. Quality control and assurance are essential components of this process in order to ensure the integrity of the product. This article will discuss why quality control is so important in PCB manufacturing, the different tests and verifications that are utilized in the process. We will explore how rigorous testing and verification of components can ensure a reliable product that meets customer goals and standards.
Why Quality Control is Important?
Quality control in PCB Manufacturing is an essential component of the process because it ensures that components and products are of high quality and perform as expected. PCBs are an integral part of many industries, include Consumer Electronics, Industrial Control, Medical Instrument, Automotive Manufacturing, Military Industry, Artificial Intelligent playing a key role in crucial areas. Without quality control, PCBs may be assembled incorrectly, and the end result could be a product that does not meet customer requirements. Quality control also verifies the performance of components such as copper materials, glass fibers, and conductive epoxies, in order to ensure a reliable product that meets industry standards. Quality control not only helps maintain visibility into the manufacturing process and ensure dependable working conditions, but also guarantees the output of reliable products.
Different Tests and Verifications in PCB Manufacturing
There are several tests and verifications for PCB manufacturing which are critical to ensuring quality control. These tests and verifications include Automated Optical Inspection (AOI) Testing, Microscopic Examination, Impedance Testing, Electronic Test, and Final Product Inspection.
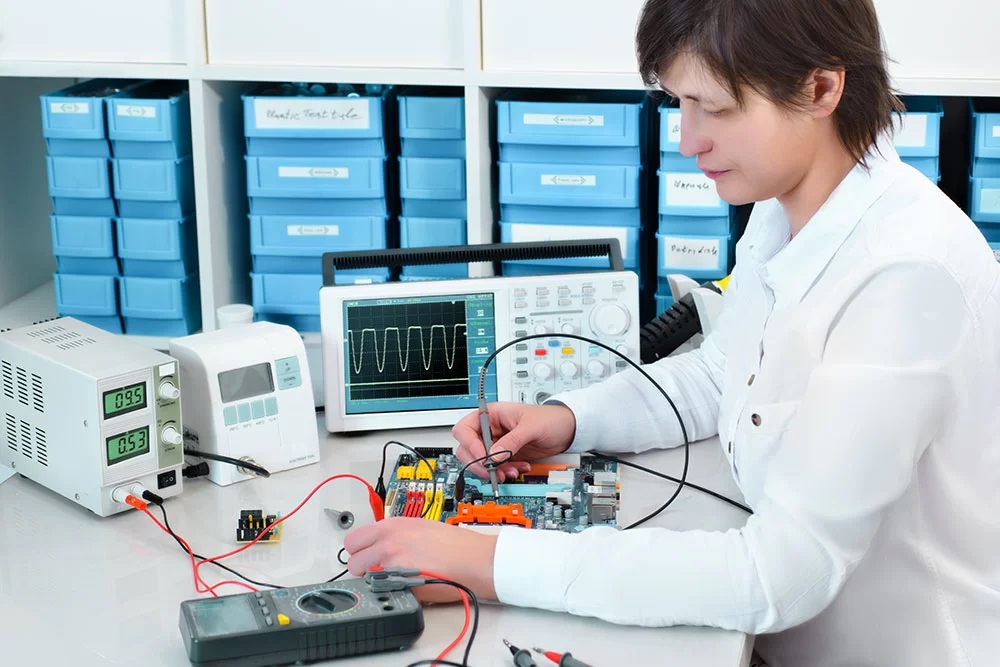
AOI Testing
Automated Optical Inspection (AOI) Testing is a key component of quality control in PCB Manufacturing. AOI Testing uses an automated visual inspection of the printed circuit in order to detect any irregularities, defects, or inaccuracies. This process uses an advanced camera system that autonomously scans the device to detect any problems that human eyes cannot see, thereby saving time and resources in detecting any problems on the PCB board. AOI Testing can detect discrepancies in size and shape, component skew, and missing or incorrect pads.
Microscopic Examination
Microscopic Examination is another important component of quality control in PCB Manufacturing. This type of examination is used for quality control (QC/QA) and failure analysis (FA). It is typically carried out using digital microscopes, which allow for high-quality imaging of all the components on the board. Microscopic Examination can measure the sizes of all individual components, check the surface quality, and identify any defects or discrepancies. This helps to ensure that the circuit board will perform as expected and that all components are up to industry standards and customer requirements.
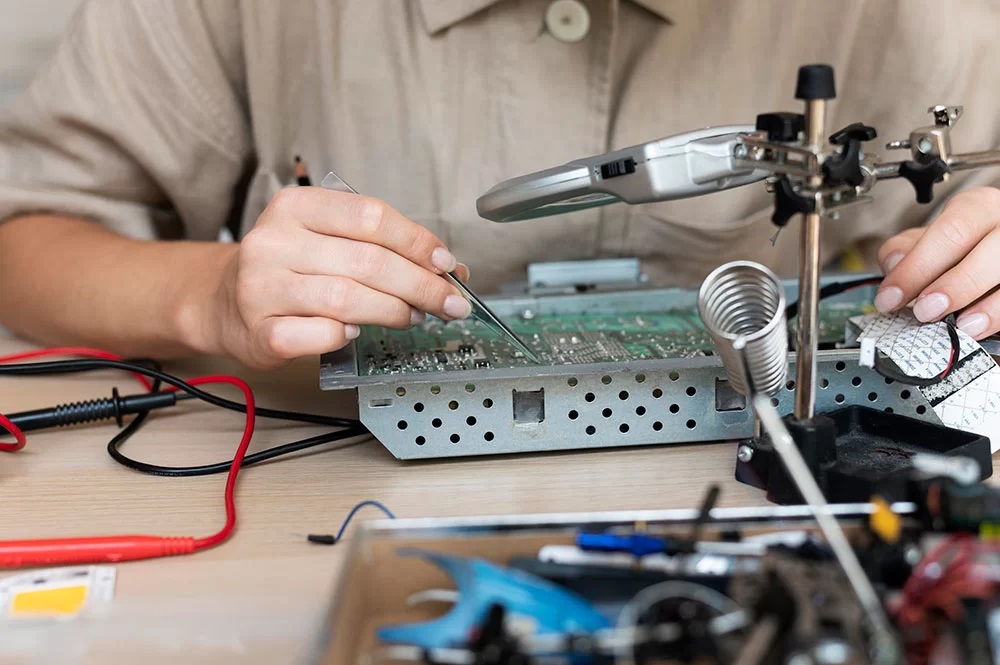
Impedance Testing
Impedance Testing is a critical component of quality control for PCB Manufacturing. Impedance Testing involves measuring the impedance of a transmission line on a printed circuit board (PCB) in total isolation from any other transmission line on the board. This helps to measure the impedance of certain traces in order to make sure they are within the limits given by the designer. This is typically done using a network analyzer, which measures the capacitance, inductance, and resistance of components. Impedance Testing helps to verify the integrity of the traces to ensure that the device will function as expected and meet the quality standards that were set out by the designer.
Electronic Test
Electronic Test is another important component of quality control for PCB Manufacturing. This type of test is used to ensure that components are performing as expected. Electronic Test can include Capacitance Testing, Resistance Testing, Comparative Testing, Continuity Testing, Flip Test, Clamshell Testing, Adjacency Testing, and Flying Probe Testing. This type of test helps to verify component values and detect any errors or discrepancies that may have been overlooked in the design stage. Additionally, electronic testing can also verify the accuracy of components such as capacitors, resistors, and transistors to ensure peak performance and reliability of the device.
Final Product Inspection
Final Product Inspection is a key component of quality control in PCB Manufacturing. This type of inspection verifies all criteria that the board must comply with prior to shipping. This type of inspection helps to ensure that the board is of high quality and ultimately meets customer expectations.
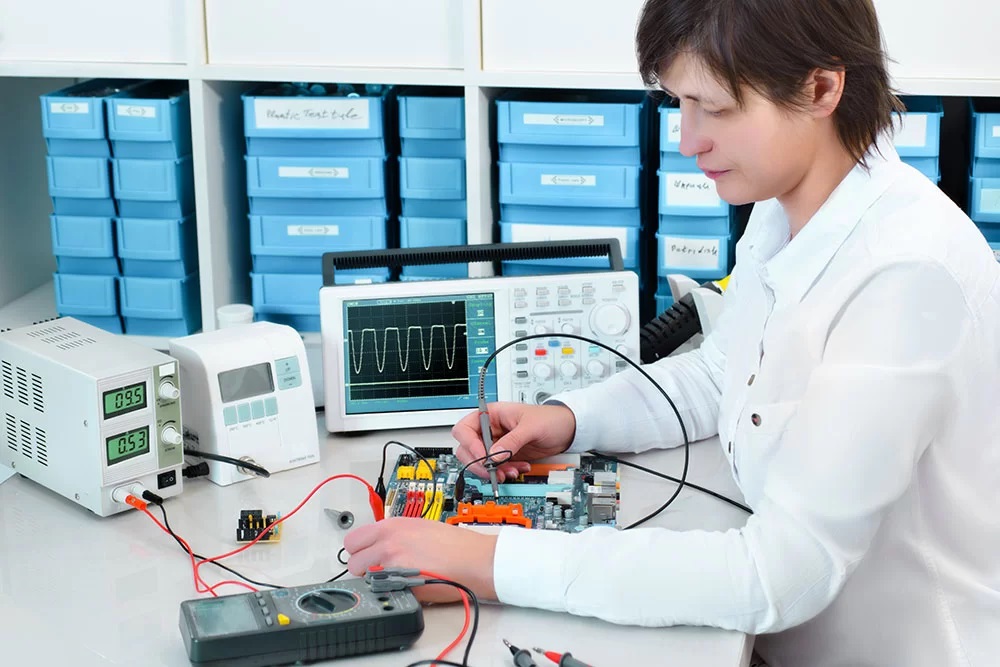
Tests and Verifications for PCBA (Assembly)
Different tests and verifications are used for testing and verifying a Printed Circuit Board Assembly (PCBA). These include First Article Confirmation, Automated Optical Inspection (AOI) Testing, Dub Plug-in Inspection, Function Test, and Final Product Inspection.
First Article Confirmation
First Article Confirmation is an essential step in the testing and verification of a Printed Circuit Board Assembly (PCBA). This process involves comparing the actual components that are used in the assembly with the reference design to check for accuracy in terms of size, Quantity, type, and specification. This enables the manufacturer to quickly and accurately identify any discrepancies or incorrect components that may have been used in the assembly. Additionally, it also helps to ensure that the products match the customer’s requirements and specifications. First Article Confirmation is an important step in quality control and a vital part of the process for PCBA manufacturing.
AOI Testing
Automated Optical Inspection (AOI) Testing is a critical component of quality control in PCBA Manufacturing. AOI Testing uses an automated visual inspection of the printed circuit in order to detect any irregularities, defects, or inaccuracies. This process uses an advanced camera system that autonomously scans the device to detect any problems that human eyes cannot see, thereby saving time and resources in detecting any problems on the PCB board. AOI Testing can detect discrepancies in size and shape, component skew, missing or incorrect pads, and missing components. This type of testing helps to identify any problems before mass production begins, thus improving the quality and reliability of the final product.
DIP Plug-in Inspection
DIP Plug-in Inspection for PCBA manufacturing is a highly reliable method to ensure quality control. The process involves inserting each component into a DIP socket and using automated optical inspection (AOI) to scan and verify that each component is correctly placed, and meets the required specifications. This system eliminates the need for manual inspection, providing much more accurate results and reliable quality control. By using the DIP Plug-in process, manufacturers are able to quickly and accurately assess the quality of the PCBA and ensure their products meet the highest standards of quality.
Function Test
Function Test for PCBA manufacturing is a critical step in the overall quality assurance process. The purpose of this test is to identify any problems or issues in the board’s functionality, before the product is released. The test can include a range of tests such as functionality testing, power-on testing, and current consumption testing. If any issues are detected, the manufacturer can address them before product shipping, resulting in a more reliable product and greater customer satisfaction. With the Function Test for PCBA manufacturing, manufacturers can ensure that their products are of the highest standard and meet their customers’ expectations.
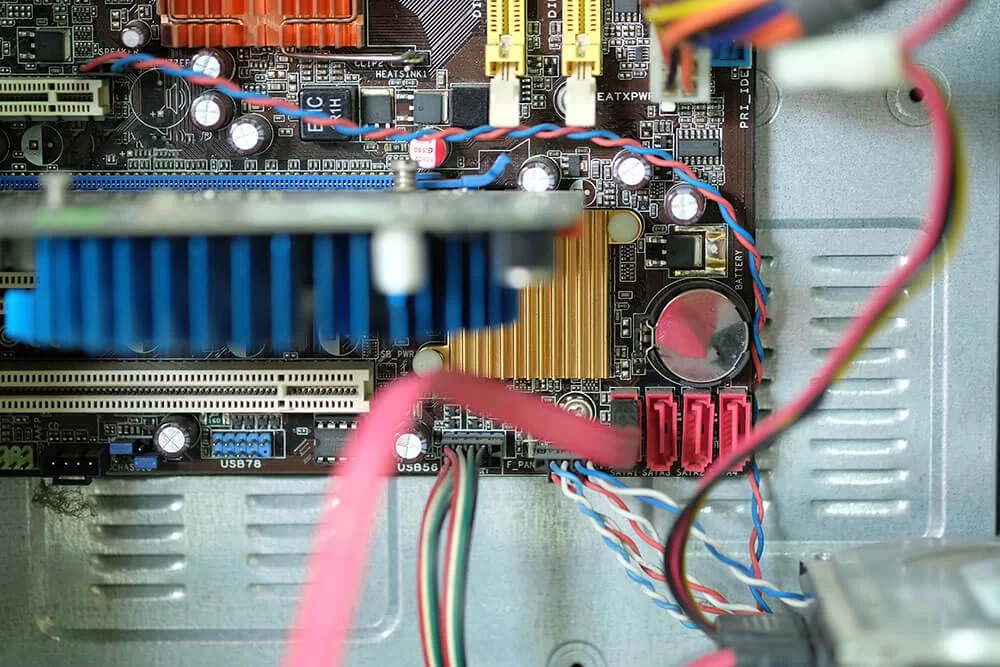
Final Product Inspection
Final Product Inspection for PCBA manufacturing is the final step in the quality assurance process. This important procedure ensures that all products are inspected thoroughly before shipping. The inspection includes a visual inspection of the product, as well as function testing and AOI inspection. By performing these thorough checks, manufacturers can ensure that all products meet the highest standards and are free of any defects or discrepancies. Final Product Inspection for PCBA manufacturing is essential to guarantee a reliable and quality product that customers will be satisfied with.
Quality of the manufacturing process
In order to ensure the quality of PCB manufacturing, a fool-proof and leak-proof control of equipment is essential. IT management should be promoted, such as tracing, mixing material, PCN, and abnormal quality control. The process should also involve the mechanism system of dedicated person and dedicated post establishment and maintenance, staff introduction, training, education, retention, and promotion planning, implementation of baseline, red line, and rolling fixed-line case studies, prenatal evaluation of the design, identification and prevention of risk points, and clear management responsibilities, guided by KPI. With these in place, it is possible to reach an optimal level of manufacturing quality.
Benefits of Topfast for Quality Assurance and Control
NETPCB offers an one-stop solution services include comprehensive Quality Assurance and Control of PCB manufacturing service with a range of benefits. They check customers’ engineering documents to ensure accuracy and quality, and provide suggestions for improvement. Additionally, they use Automated Optical Inspection (AOI) to inspect all products, helping to identify issues and verify quality. Finally, they send photos of the product to the customer before it is shipped for a final confirmation that the product has met their requirements and specifications. These rigorous steps ensure that the highest quality PCB is delivered to the customer. Beside that, before beginning the build process of a prototype circuit board, be sure to check the common mistakes to avoid in order to ensure a successful build.