Are you curious about the FR4 material that is most often used in printed circuit boards? You’re not alone – this versatile material is one of the most popular options for PCB prototypes and PCB assembly because of its many advantageous qualities. In this article, we will discuss why FR4 is so popular, the types of applications it is used in, and how it compares to polyimide materials.
What is FR4 for PCB fabrication ?
FR4 is a flame-resistant, strong and waterproof material that is composed of epoxy resin and glass fabric composite. It is an ideal material for producing rigid circuit boards.
FR4 provides excellent insulation between copper layers and minimizes interference. It usually comes with copper traces to offers good signal integrity for reliable and accurate results in single or multi-layer boards.
Why FR4 is popular for PCB prototyping and PCB assembly?
FR4 is a popular option for prototyping and PCB assembly for a variety of reasons. One of its main benefits is its flame resistance, which increases the safety of electronic components used in PCBs.
Additionally, its strong and waterproof composition makes it ideal for production of rigid circuit boards. The good insulation between copper layers minimizes interference while the good signal integrity ensures reliable and accurate results.
Furthermore, the presence of copper traces allows for an easier and faster assembly process, making FR4 a preferred material particularly for prototyping purposes.
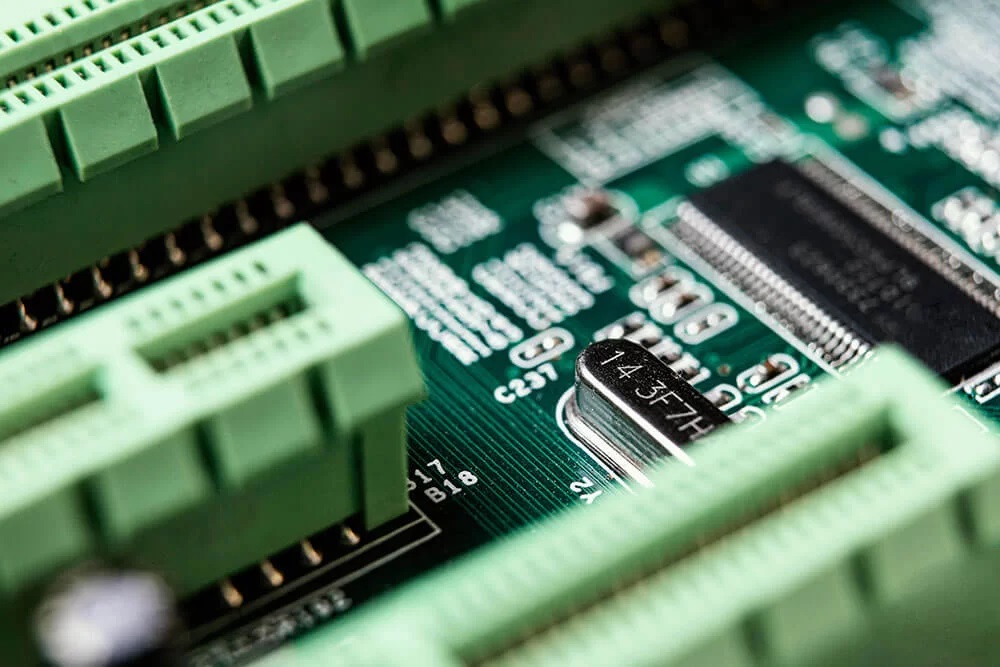
Advantages of the FR4 Circuit board
- Good signal integrity
- High insulation properties
- Higher temperature stability
- Flame resistant
- Waterproof resistant
- Higher level of complexity in design
- Cost reduction due to increased durability
FR4 for what kind of PCB applications
FR4 material is perfect for a wide range of PCB applications. It is commonly used in single or multi-layer boards and can handle a variety of board modifications.
It is an affordable option for creating printed circuit boards and its flame-resistant properties make it a safe choice for electrical enclosures ensuring the components used in the boards are protected.
FR4 is also suitable for industrial and commercial applications that require the use of rigid boards, due to its strong and waterproof nature that allows for efficient manufacturing. With its good insulation and signal integrity, this material is an ideal choice for reliable and accurate results.
FR4 vs Polyimide
When comparing FR4 and polyimide materials, it is important to note that polyimide has certain advantages over its counterpart. Polyimide is used in the production of flexible PCBs because of its ability to be bent or twisted without breaking.
Additionally, polyimide offers increased corrosion resistance over long periods, meaning it can be used in a variety of environments. However, polyimide is generally more expensive than FR4 and tends to be more difficult to work with.
FR4 has a greater signal integrity and flame resistance which makes it the preferred choice for rigid PCBs. Combined with a flexible polyimide material it’s also used in Rigid-flex PCB manufacturing.
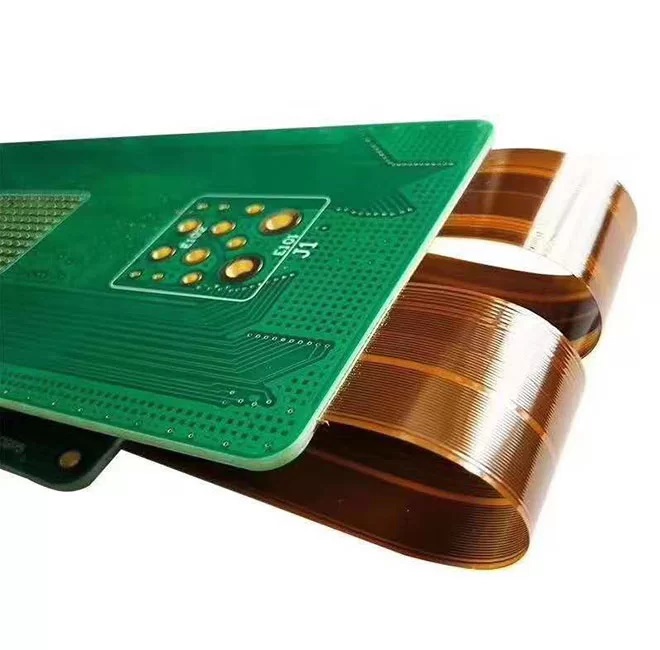
Alternative to FR4 material for PCB Fabrication
CEM-1, a much cheaper alternative
CEM-1 is a paper-based material commonly used as an alternative to FR4 for Printed Circuit Board (PCB) manufacturing. As it is a cheaper material than FR4, CEM-1 boards provide an economical solution when cost is a determining factor in design.
Despite being a cheaper material, CEM-1 boards have a similar dielectric constant (K) value, CEM-1 material provides less resistance to heat which allows for effective heat dissipation in comparison to FR4 boards.
In terms of composition, CEM-1 boards are manufactured from a combination of paper, woven glass epoxy, phenol compounds and layered resins. This provides higher flexibility and lower levels of water absorption when compared to FR4.
CEM-3, the best alternative
CEM-3 is also a paper-based material that is used as an alternative to FR4 in Printed Circuit Board manufacturing. Compared to FR4, CEM-3 is cheaper and provides a very similar level of performance.
Additionally, due to their material composition of paper, woven glass epoxy and phenol compounds, CEM-3 boards are lightweight. Furthermore, CEM-3 is able to provide superior thermal and mechanical shock resistance when compared to FR4.
Despite the low cost of CEM-3 compared to FR4, the performance it offers makes it an attractive option for many PCB designs.
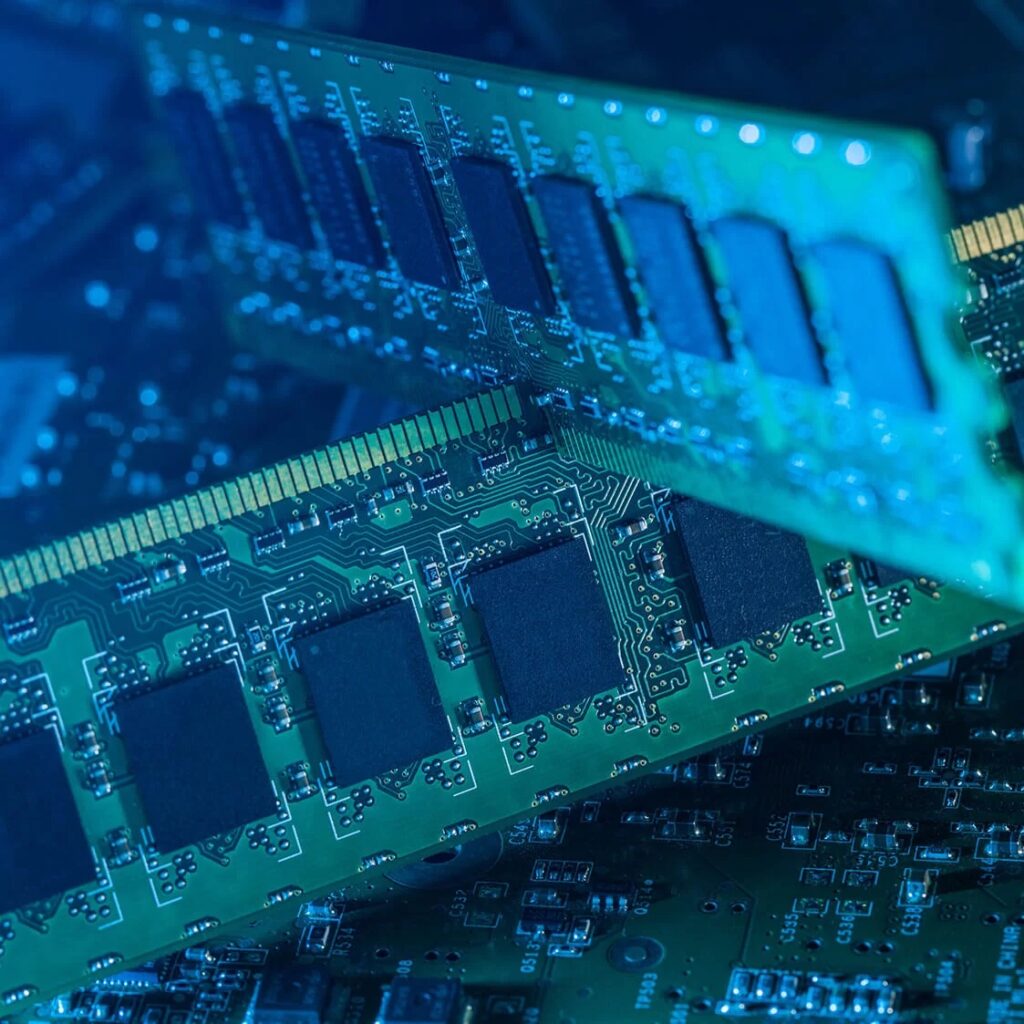
The Downside of the FR4
The main downside of FR4 for Printed Circuit Board (PCB) manufacturing is its relatively high dielectric loss and high dissipation factor. These characteristics can introduce unwanted distortions in the board’s signal which may limit its performance.
Additionally, FR4 is not suitable for use with high-speed or high-frequency applications and its material can be damaged when exposed to high power, voltage, or strong heat.
Furthermore, FR4 has a limited working temperature range of -55°C to +130°C which can cause issues for PCB designs that require extreme temperatures. Therefore, FR4 may not be suitable for all PCB applications and could lead to board failure if the proper precautions and considerations are not made.